Innovation as a driver for more sustainability
More than 200 patents and designs for our own developments over the past decades underscore the central importance of innovation for MEISTERWERKE: they strengthen the company's competitiveness in the market. However, in addition to the focus on development of the criteria of design and product and assembly properties, sustainable aspects including the conservation of resources are also gaining in importance today. One MEISTERWERKE product that optimally takes into account the combination of these aspects and demonstrates that market success and sustainability can go hand in hand is the Lindura wood flooring introduced in 2014.
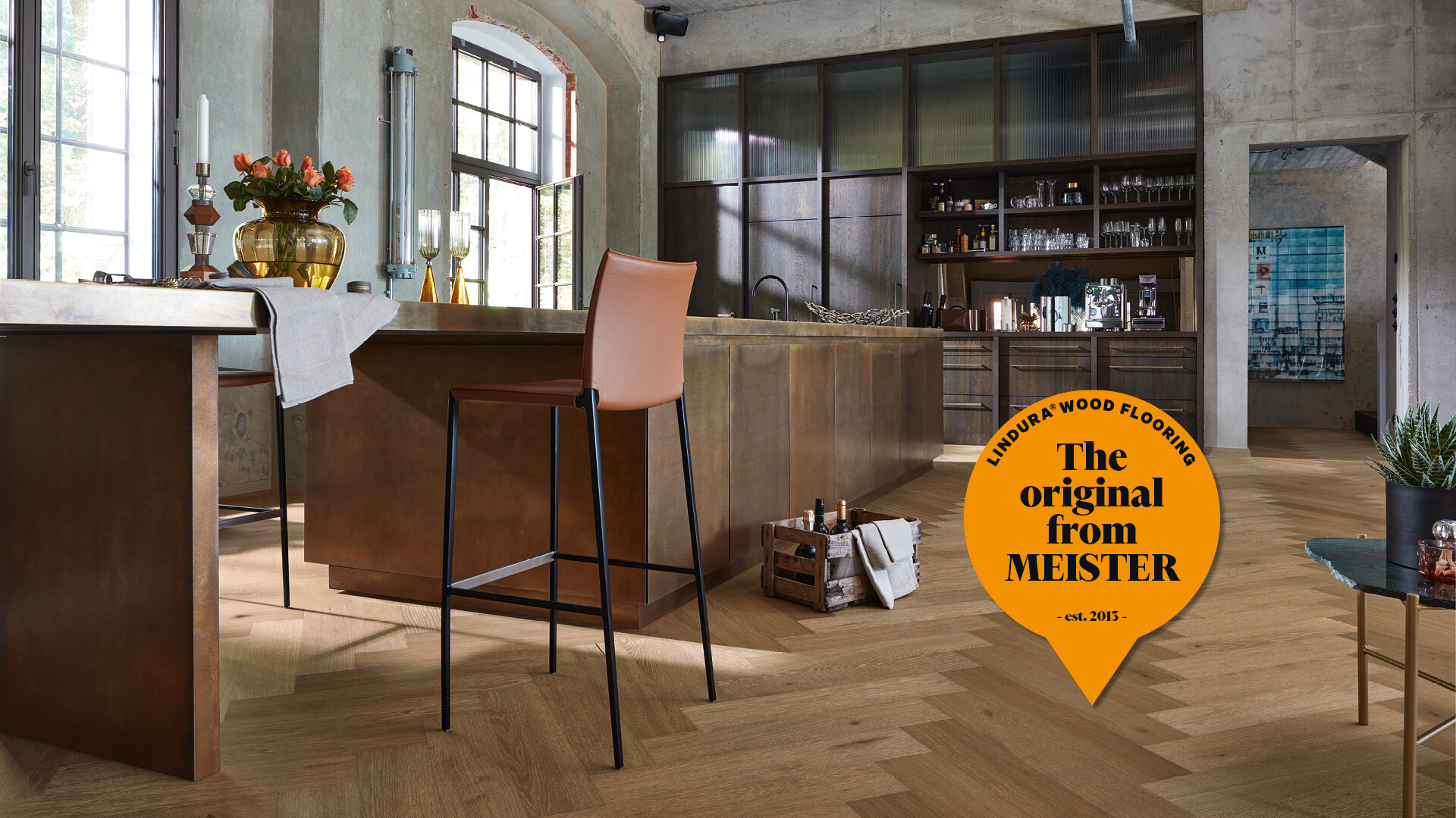
Lindura: wood flooring of the future
The basis of Lindura wood flooring is innovative “wood powder”, a material mixture of fine wood fibres, mineral components and other natural additives developed by Swedish MEISTERWERKE partner Välinge. In the production process, pressure and heat is applied to fuse the wood powder together with a real wood covering layer, an HDF middle layer, and a backing. This creates an attractive wood flooring that, compared to a multi-layer parquet flooring, requires only an eighth of the wood needed for the surface and also has significantly better product properties, e.g. in terms of dent resistance. With respect to the current scarcity of resources, Guido Schulte is certain this is a product with great future potential. “Lindura shows that more careful use of valuable wood resources is not synonymous with sacrificing the look, feel and product properties of wood. Quite the contrary: by using innovative material compositions and manufacturing processes, we can combine the beauty and natural surface aspects of wood with improved properties that make wooden flooring even more suitable for everyday use.” Lindura has been honoured with multiple awards, including the Gold Innovation Award at the HolzLand & MDH Expo in Hanover (2014) and the prestigious Schweighofer Prize in the “Innovation” category (2015).
“Lindura shows that more careful use of valuable wood resources is not synonymous with sacrificing the look, feel and product properties of wood. Quite the contrary: by using innovative material compositions and manufacturing processes, we can combine the beauty and natural surface aspects of wood with improved properties that make wooden flooring even more suitable for everyday use.”
Not only is the Lindura product itself sustainable but also the manufacturing process. For production of the wood powder which MEISTERWERKE has been manufacturing in-house since 2015, most of the wood fibres that are produced in the company's own moulding production are, for example, fed back into the production cycle as a residual material. With this, MEISTERWERKE is also following the recommendations of the Charter for Wood 2.0, an initiative of the German Federal Ministry of Food and Agriculture, which recommends the wood and forestry sector adopt, among other things, improved material efficiency in the use of materials and energy as well as optimise recycling of valuable materials from production processes or old wood from a wide range of areas of use.
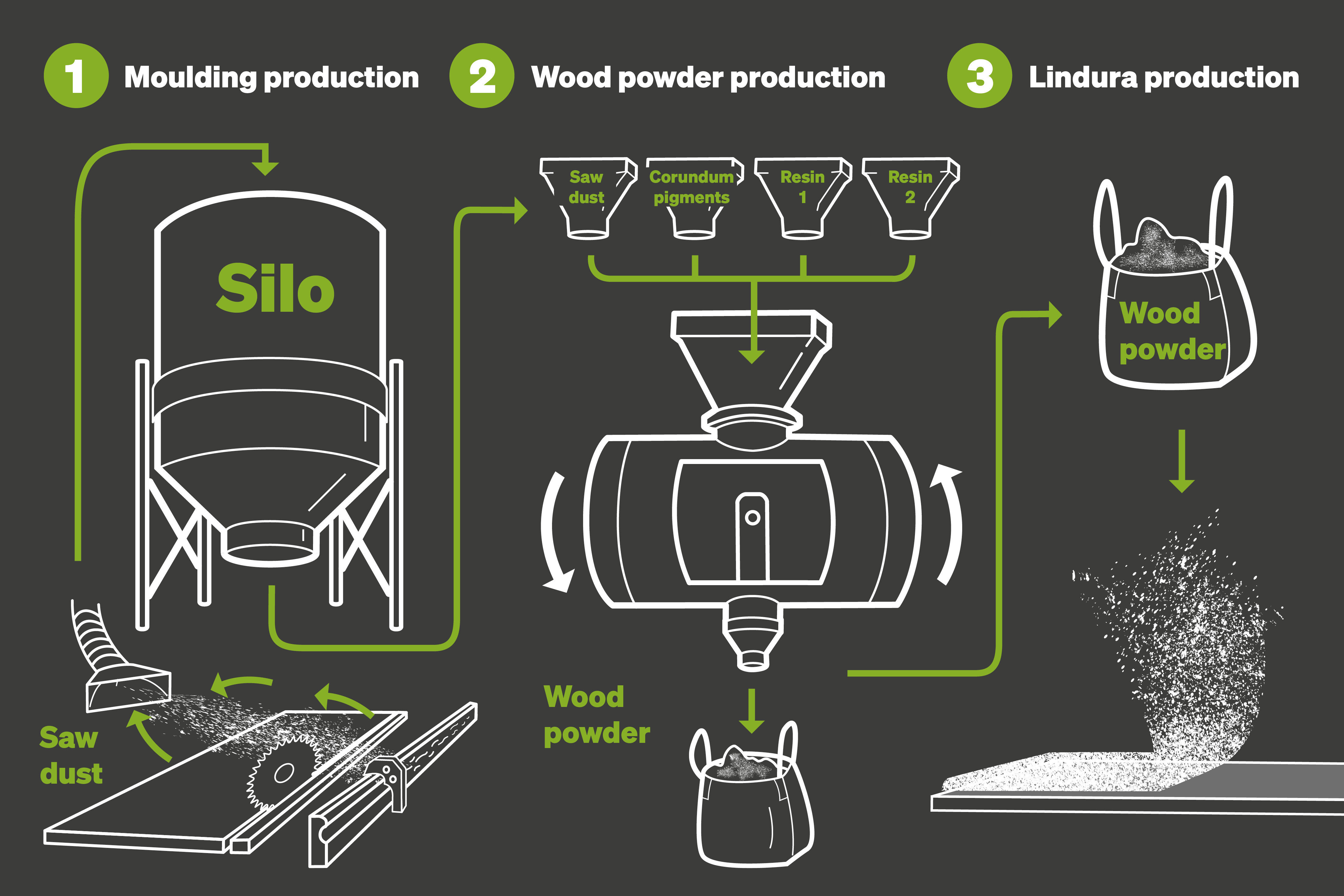
Designing sustainable products and processes
To be able to sustainably extend carbon cycles, use of the available raw materials must be optimised. This is demonstrated not only by the example of Lindura but also by the “MeisterPanels. craft” collection of real wood panels launched onto the market in early 2021. Here, wood covering layers that cannot be used for parquet production due to deviating specifications or dimensions are given a special deeply structured surface and can thus be used for a new purpose: processing into wall and ceiling panels. At the same time, MEISTERWERKE is optimising its use of raw materials – an issue that is always on the company’s agenda. One example of successful optimisation measures is the “click technique” developed in-house for the production of laminate flooring: by staggering the cutting of the boards, the geometry of the click profile is already predefined when the planks are cut apart. Waste can thus be reduced by approx. 4 percent, and product output can be increased by approx. 4 percent for common HDF board formats.
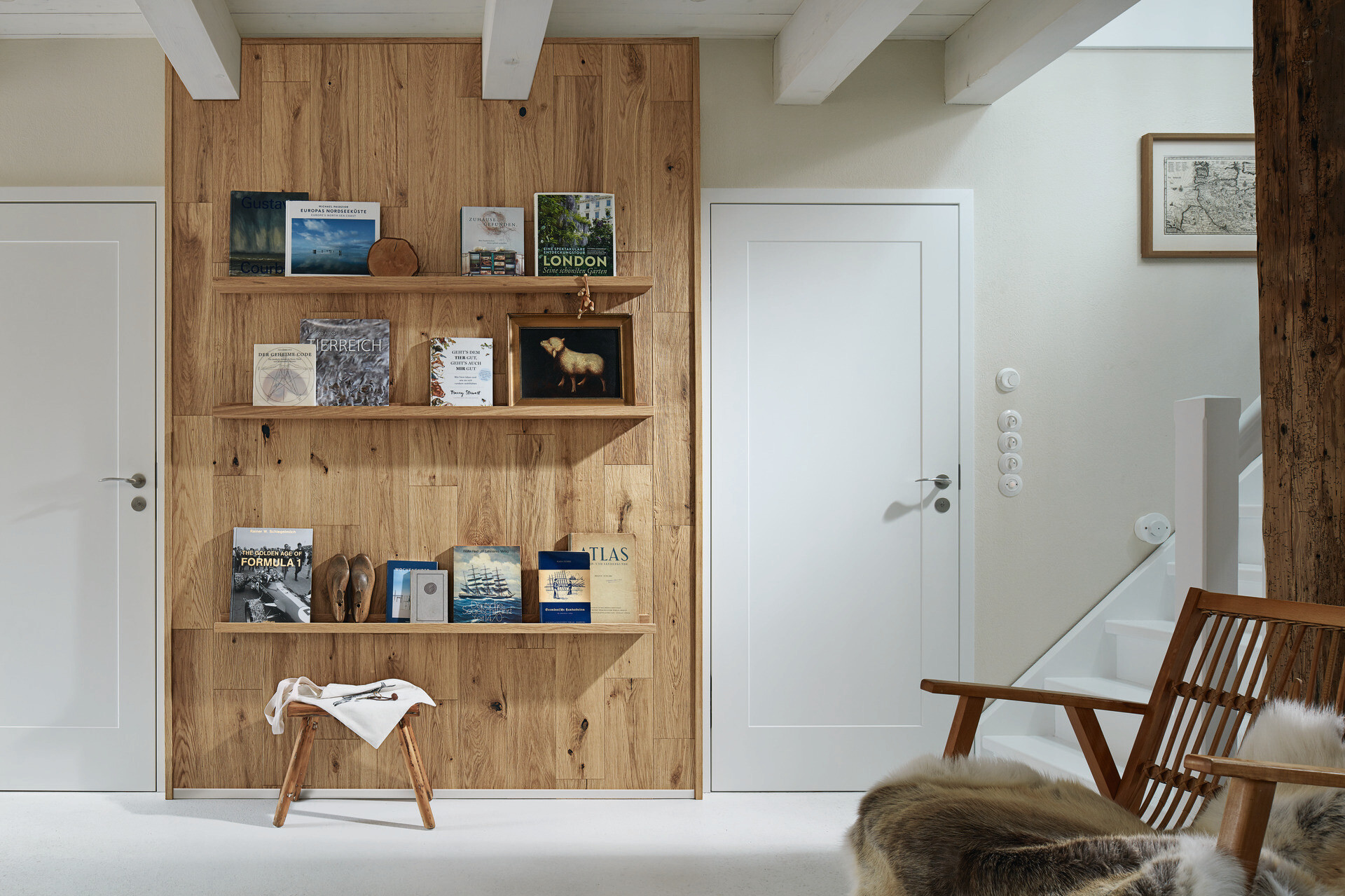
Sustainable use of wood resources also concerns MEISTERWERKE beyond its core business – the manufacture of products for floors, walls and ceilings. Based on the patent of a former employee, production is moving forward for a biodegradable cover made of wood that protects against browsing by wildlife and is to be used in reforestation of forests and tree stands. This innovative product replaces plastic sheaths that are currently used and which must be removed and collected after roughly 7 to 8 years – an immensely time-consuming process for forestry management.
MEISTERcycle – closed-loop recycling
Optimising the use of raw materials within the entire value chain plays an important role at MEISTERWERKE – even beyond the company’s own production facilities. Whereas plastic waste produced during the manufacture of design flooring is already being collected, sorted by type, and returned to the individual suppliers for recycling, the handling of offcuts and waste produced during installation of flooring – as well as disposal of the products after they are removed at the end of the life cycle – are often not transparent. MEISTERWERKE is committed here to greater sustainability in the entire system: With the revision of the “MeisterDesign. rigid” product range in early 2022, a return and recycling system is being installed for these products that will enable waste to be returned to the production cycle. MEISTERWERKE is organising the entire process chain here, starting with providing the collection boxes at the participating specialist retailers and ending with the return transport to the individual suppliers.
“Product development plays a decisive role today in managing resource efficiency, because efficient recycling processes have to be taken into account from the outset. This presents us with new challenges as products become more complex with more extensive functions,” said Volker Kettler, Director Product Management at MEISTERWERKE.
“The demands on products with respect to ecology and sustainability will continue to increase in the future, which is why we must consistently pursue holistic approaches like those we have now implemented with MeisterDesign. rigid, across the entire product portfolio.”
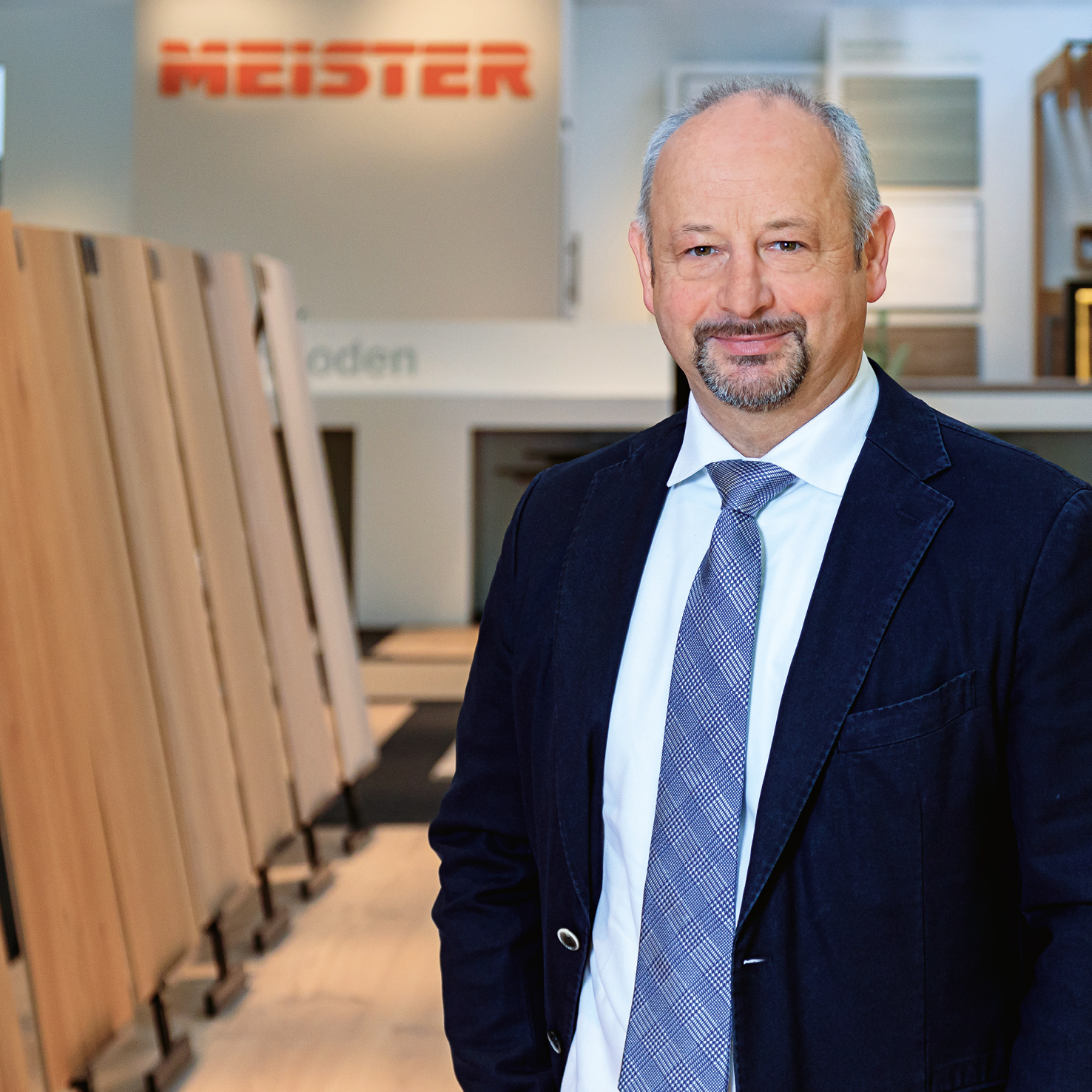